The Rise of Modular Construction: Solutions for Cost and Labor Challenges
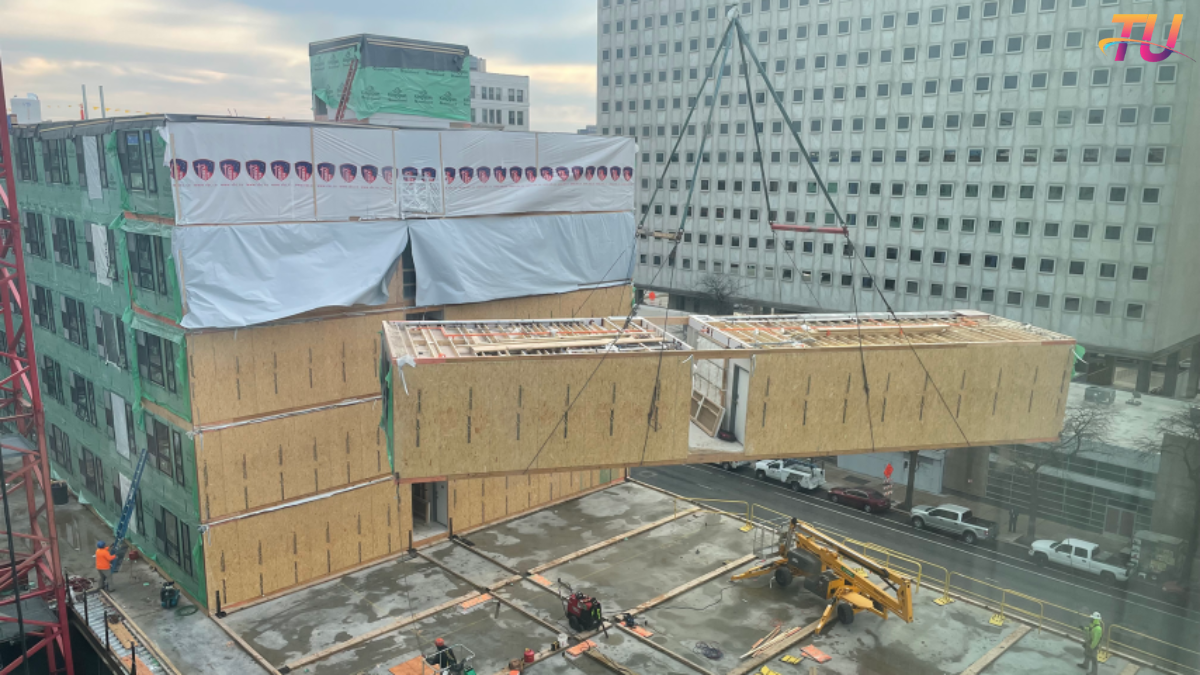
Modular construction, once viewed as a niche solution, is quickly becoming a mainstream approach in the building industry. As builders and developers look for ways to cut costs and address labor shortages, modular methods offer a compelling solution. By constructing building modules in a factory setting before assembling them on-site, companies can save time and reduce waste. For developers, working with construction estimating companies that specialize in modular projects can be critical to accurately forecasting costs and achieving efficiency.
1. What is Modular Construction?
Modular construction involves manufacturing sections, or “modules,” of a building off-site in a controlled factory environment. These modules are then transported to the construction site and assembled into a complete structure. Unlike traditional methods, where everything is built from scratch on-site, modular construction allows for more consistent quality control and faster project timelines. Modular techniques can be applied to various types of buildings, from single-family homes to multi-story residential buildings, hotels, hospitals, and even schools.
One of the biggest benefits of modular construction is the ability to work on multiple aspects of the project simultaneously. While the site is prepared and foundations are laid, modules can be manufactured in the factory, drastically reducing construction time. Once the modules are complete, they are delivered to the site, where they’re quickly assembled, speeding up the overall project.
2. Solving the Labor Shortage with Modular Construction
Labor shortages are a growing challenge in construction. Skilled workers are in high demand, and finding enough talent to meet project needs can delay timelines and drive up costs. Modular construction addresses this issue by shifting much of the work to a factory setting, where tasks are streamlined and labor needs are reduced.
In a factory environment, modular construction companies can employ fewer workers to complete the same tasks that would require more on-site labor. The controlled conditions also mean that workers are less exposed to hazardous elements like extreme weather, reducing health and safety risks. With fewer people needed on-site, companies can minimize the impact of labor shortages and improve project reliability.
3. Cost Efficiency and Waste Reduction
One of the primary advantages of modular construction is cost efficiency. Building in a controlled environment reduces waste, as materials are used more precisely, and leftovers can often be recycled for future projects. Factory production also minimizes the likelihood of costly delays due to weather or logistical issues. With shorter construction timelines, developers can realize savings on labor and equipment rentals, while also bringing buildings to market faster.
Additionally, modular construction minimizes disruptions to the surrounding community. Since the majority of construction happens off-site, there’s less noise, dust, and traffic at the building site itself. This makes modular construction an attractive option for projects in dense urban areas or areas with strict building regulations.
4. Maintaining Quality and Precision in Factory-Built Modules
One of the key benefits of modular construction is the high degree of quality control achievable in a factory setting. Unlike traditional on-site construction, where quality can vary due to weather and other uncontrollable factors, modular construction allows for more precise quality checks. Each module undergoes a rigorous inspection process before it leaves the factory, ensuring that building standards and specifications are met consistently.
Furthermore, modular construction often utilizes sustainable materials and energy-efficient designs, making it a more eco-friendly option. Modules can be designed with optimal insulation, energy-efficient windows, and sustainable materials that reduce the building’s overall environmental footprint. This commitment to quality and sustainability has positioned modular construction as a solution for those seeking both durability and environmental responsibility in their projects.
5. Role of Estimation and Takeoff Companies in Modular Construction
Accurate budgeting and resource planning are essential for any construction project, but they become even more critical in modular construction. Since much of the work is done off-site, the precision of material estimates directly affects project timelines and costs. Construction takeoff companies play a vital role here, as they assess the materials needed for each module, ensuring that quantities align with the design specifications and budget constraints.
Collaborating with experienced construction takeoff companies can help developers streamline procurement and avoid material shortages or surpluses. Accurate takeoffs are essential to maintain the factory’s production flow, ensuring that modules are completed on schedule and delivered to the site without delays. This level of efficiency allows developers to complete projects faster and within budget, maximizing the benefits of modular construction.
The Future of Modular Construction
Modular construction is increasingly recognized for its potential to address many of the industry’s pressing challenges, from labor shortages to cost control and sustainability. By embracing modular methods, the construction industry is better equipped to adapt to changing demands, including the need for affordable housing and quicker project timelines. As technology advances and building practices evolve, modular construction is poised to become a standard approach for a wide range of projects.
In a rapidly evolving industry, modular construction offers a path to greater efficiency, cost savings, and adaptability. By working with specialized partners, such as construction estimating companies and takeoff specialists, developers can ensure that their modular projects run smoothly and meet quality standards. With modular construction, the industry is not just keeping up with demand—it’s setting a new standard for innovation and efficiency.
0 Comments